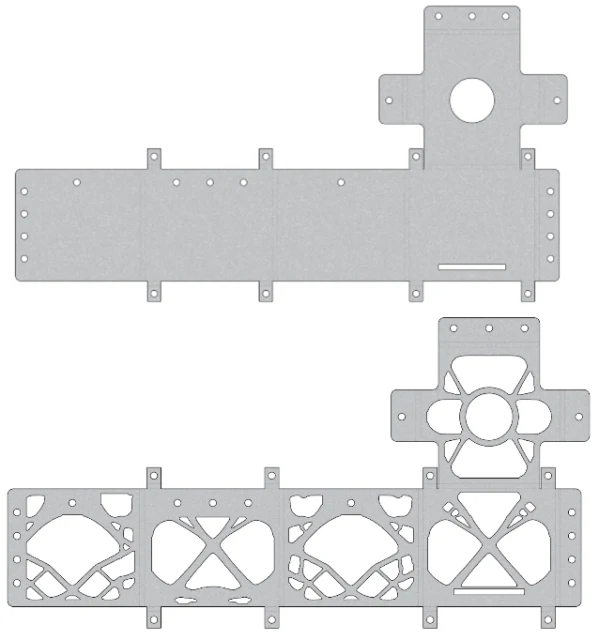
Fastest Ways to Optimize Designs for Manufacturing with Generative Design on the Cloud
- 3D modelingExperience
- March 31, 2021
New cloud CATIA-based app offers two different optimizers for sheet metal.
Generative design is a perfect example of technology high in promise but with a future delivery date. Letting computers actually assist with design work—the “A” in Computer-Aided Design—has the potential to upend the role of the design engineer. But achieving this potential, in practice, is not straightforward.
One of the long-standing challenges of generative design is manufacturability. The perfect part is useless if there is no way to make it. At its core, the generative design does not care how a part is made. With algorithms inspired by nature—like the way human bones grow and heal—generative design is focused on producing a passable shape—not a manufacturable part. That is why it winds up with those unmistakably organic geometries.
Typically, this means that generative design is incompatible with subtractive manufacturing. Additive manufacturing is often the only way to produce generatively designed parts, but this comes with its own challenges and limitations. Some developers of generative design software get around this problem by forcing designs to adhere to manufacturing constraints, but the gain for manufacturability comes at a cost in optimization.
This month, Dassault Systèmes is debuting a generative design app that offers another solution to the technology’s manufacturing woes. The CATIA-based Structural Generative Design app provides two types of generative design for sheet metal.
Sheet Metal Generative Design
Generative design is typically performed in 3D—i.e., generative design algorithms run on solid elements such as tetrahedrons. Dassault Systèmes’ new solution is based on shell elements, which are used to analyze thin structures like sheet metal.
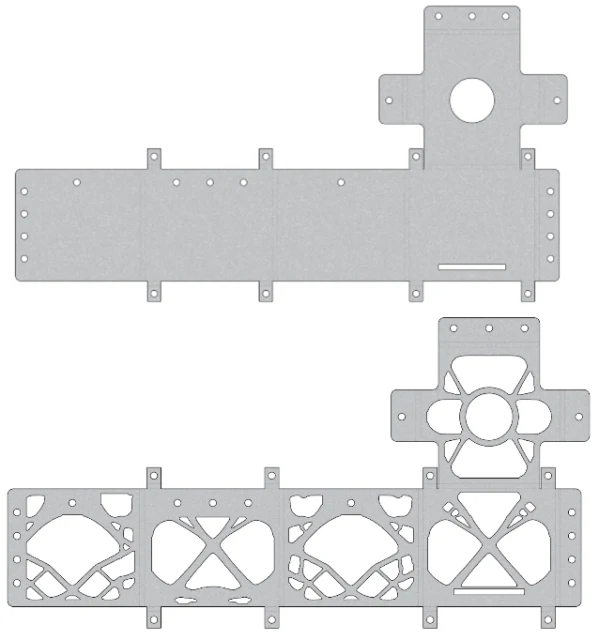
Structural Generative Design offers two unique types of sheet metal optimization. The first is akin to a conventional topology optimization, in which material is removed from the original geometry to achieve a lighter-weight part that conforms to specified structural requirements. In sheet metal, this amounts to cutouts in areas with low stress. Dassault Systèmes calls this technology surface topology optimization.
Dassault Systèmes’ Nicolas Guerin, CATIA R&D Portfolio Manager, described this technology to engineering.com with the example of a CubeSat. The small satellite is contained in a sheet metal enclosure which could be made lighter with Structural Generative Design. Every gram matters in aerospace and leaving excess material on Earth could not only save launch costs but can also allow more room for scientific equipment on board.
Before and after of a cubesat optimized with Structural Generative Design. (Image courtesy of Dassault Systèmes.)
Of course, it is imperative that the cutouts from the sheet metal enclosure do not compromise its structural performance. Because Structural Generative Design is integrated with CATIA and the rest of Dassault Systèmes’ 3DEXPERIENCE cloud platform, it is easy for designers to switch from generative design to structural analysis.
“At any point you can run a simulation to make sure that whatever changes you have here have actually improved your behavior,” Guerin says. “It’s actually very fast to do that because behind the scenes are shell elements, which take much less computation than solid elements. This allows you to speed up the typical design simulation iteration.”
Surface Topology Optimization is built on Dassault Systèmes’ SIMULIA simulation software, which uses the Abaqus solver, Tosca topology engine for the optimization and CATIA for the geometric modeling. Unlike some generative design software, it can force the sheet metal cutouts to be symmetrical.
Bead Optimization: All Metal, More Stiff
The second type of generative design for sheet metal is called bead optimization. This is a flavor of shape optimization that does not remove any material and hence does not change the weight of the part. Instead, bead optimization determines areas of the sheet metal that can be embossed to enhance the stiffness of a panel. This can help structurally by preventing bending or buckling, or changing the natural frequency to avoid vibration. This allows designers to improve performance without adding material.
“From a flat surface, the optimization engine decides where and what shape of bead could be put on the structure to reinforce it,” Guerin says.

Users of bead optimization can choose the optimization criterion, either to maximize stiffness or maximize the lowest Eigenfrequency, and can set their preferred emboss/deboss ranges. Users must also specify the part’s structural loads before generative design can take place.
A common problem with generative design software is that optimized parts are returned as an un-editable mesh, forcing designers to laboriously recreate the designs that the generative design software has generated. Developers seem to be wising up to this annoyance. Structural Generative Designer avoids this rework altogether by providing results in editable B-rep form.
“For each bead profile, you can overwrite it with a spline. You can smooth it or put in primitive shapes that are pure geometry [prismatic shapes] with parameters like radius,” Guerin says. “The generative design automation gives you a blueprint, and with the sheet metal reconstruction assistant, you can reverse the automation and control the shape.”
Generative Design That’s Easy to Make
The most interesting part of Structural Generative Designer—both surface topology optimization and bead optimization—is that the resulting sheet metal shapes are ready to be manufactured. The user is not confined to 3D printing. There is no need to set constraints on the generative design to ensure it can be milled. The optimized sheet metal resulting from the Structural Generative Designer can be stamped just as easily as a sheet metal part conventionally designed.
While this is not the first time we have seen generative design for sheet metal, Structural Generative Designer is, to our knowledge, the first to bring generative design for sheet metal forward into the design phase. The app, available as a service to Dassault Systèmes cloud customers, is still in its early days. It can currently only handle single parts and not assemblies. Guerin says that assemblies will be handled by the end of the year.
There is also no way to couple both forms of sheet metal optimization, i.e., produce a design with both cutouts and beads simultaneously. However, there is nothing stopping designers from using the output of surface topology optimization as the input to bead optimization, or vice versa. They will just need to be careful that the second operation did not invalidate the first.
“It’s nothing that a good engineer cannot endure,” Guerin says.
Dassault Systèmes believes this technology is helping to “move CAD from Computer-Aided Design to Cognitive Assisted Design.” To learn more about Structural Generative Designer, visit the 3DEXPERIENCE Cloud Platform website.